UAVOS Expands Helicopter Rotor Blade System Capability to Add Torsion Bar
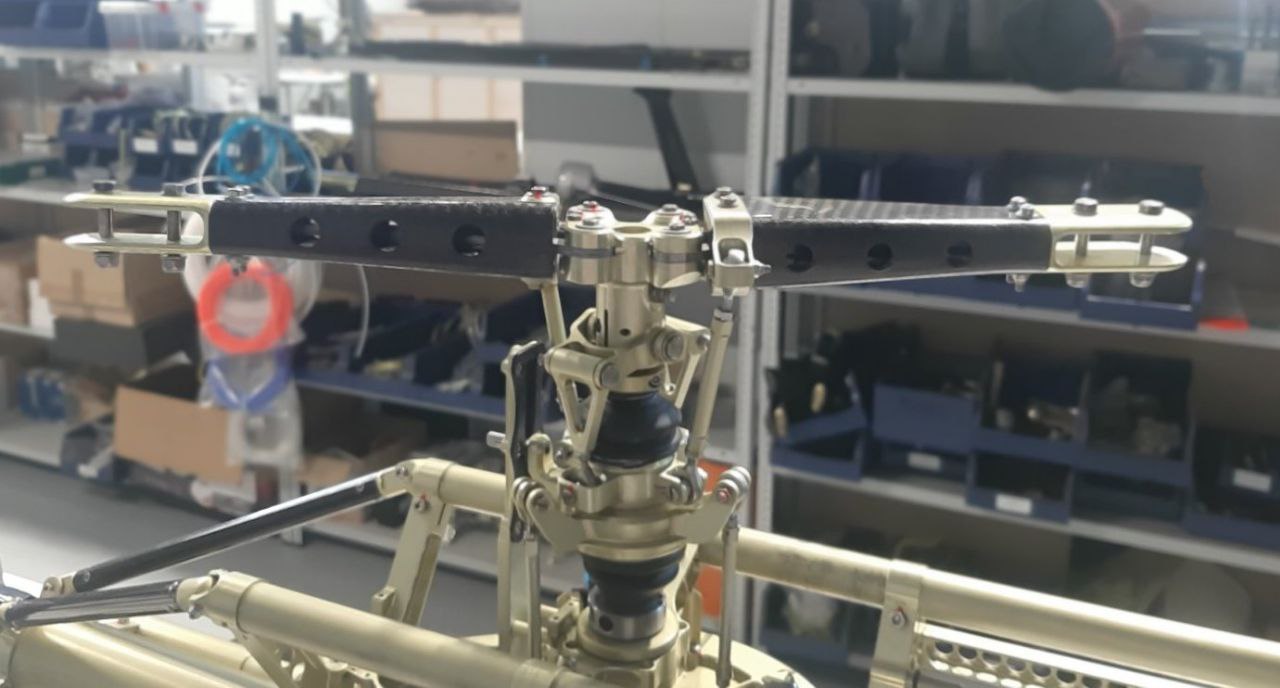
UAVOS announced that it had completed flight tests of its advanced bearingless rotor system installed on the UVH 25EL unmanned helicopter. Torsion bar is aimed to provide an effective damping action against the dynamic components of the forces and torques acting on the rotor. The new rotor design has resulted in increasing Time Between Overhauls (TBO) and therefore in low life-cycle costs, better hub design, and superior handling qualities. Torsion Bar for a main helicopter rotor is designed to be mounted on a helicopter with maximum takeoff weight of 50 kg.
Watch the video about the bearingless rotor system here: https://bit.ly/3aZ2DQE
In helicopters, the main rotor system is a critical element. To overcome many of the problems associated with the pitch bearing rotor systems, and improve the efficiency and capabilities of aircraft, many rotorcraft companies are using articulated rotors. A key element in the design of a bearingless rotor is the flexbeam. To reduce hub drag and weight, it is created light and compact and designed for centrifugal force and large elastic deflections.
UAVOS designs advanced composites rotors which feature superior fatigue characteristics, their higher stiffness- to-weight properties, their flexibility in tailoring structural characteristics, and their potential to lower production and operating costs.
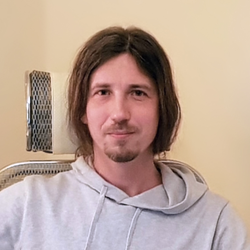
"The primary purpose of the tests is to shake out the new helicopter’s rotor system strength and measure its dynamic characteristics while the aircraft is flying,'' said CEO at UAVOS Aliaksei Stratsilatau. “The system performed extremely well over a variety of forward flight conditions as well as maneuvering up to 100 km/h. We are making great progress, and in the meantime are keeping our interested customers keenly aware of the exceptional performance that UAVOS aircraft equipped with a reliable rotor system will bring.”
14 June 2022